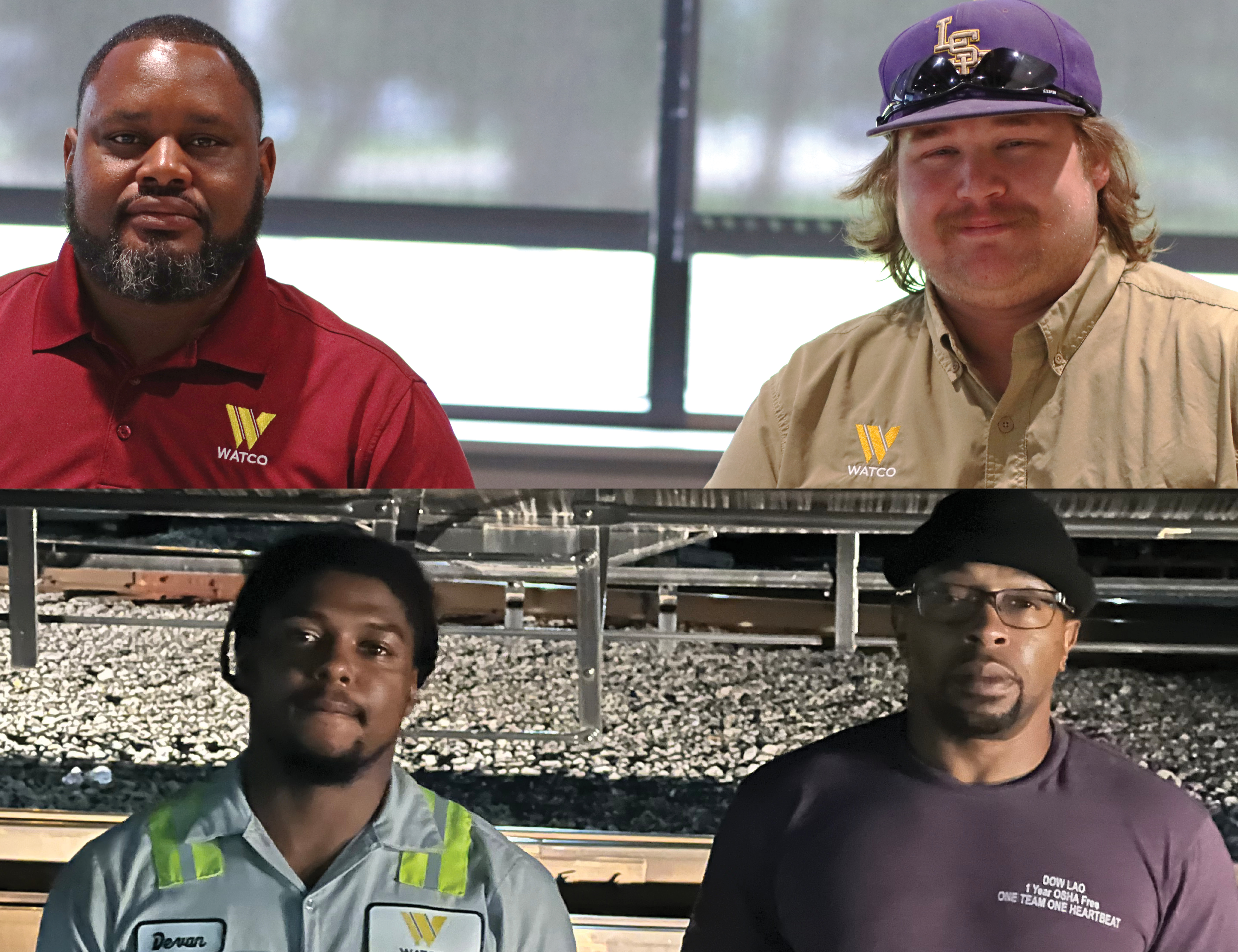
Louisiana Team Powers Through Challenges
JULY 2025 – Frigid temperatures and power outages didn’t stop the Plaquemine Industrial Rail Services team from ensuring their customer had the railcars they needed.
Even in the dead of winter, southern Louisiana rarely sees extreme cold. But in late January of 2025, those temperatures, combined with power outages, put the Plaquemine team in a difficult situation. Four team members stepped up to ensure the customer had clean railcars to load, avoiding a shutdown at the 24/7 facility.
“We had a planned outage to replace a transformer in our part of the facility,” said Drew Baldwin, former general manager who has since become terminal manager at the Port of Pine Bluff. “We planned ahead and had plenty of empty railcar inventory for a short outage, but the next day, the new transformer failed. Our stock started dwindling quickly.”
The outage only affected Watco’s area, so the other parts of the facility kept operating – and loading clean hopper cars. All the hopper cars have to be washed before they can be loaded. There are several different grades of plastic pellets produced at the plants and they can’t be cross contaminated. Medical-grade plastic can’t go into railcars that previously held food-grade plastic. And some product is accompanied by other additives that can mold if it’s not removed.
“We usually wash during the day, but that wasn’t an option due to the power outage,” Baldwin said. “Fortunately, we had the right crew scheduled for that night. They said they’d wash until the freezing temperatures made it unsafe.”
That team was Senior Trainmaster, now General Manager, Jason Green, Trainmaster Hunter Perryman, Conductor/Engineer Damian Morris, and Conductor Devan Luke. They contacted the customer, who provided two portable air compressors. And not just any air compressors. These sit on semi-trailers and can provide the pressure to pump hundreds of gallons of water through the wash rack jets each minute. Green was previously the wash rack supervisor. The others had no experience, but after a 20-minute job briefing, they were ready to get started.
Normally, two team members work on top of the cars opening hatches and inserting the water jets. Two work on the ground opening caps and rotating parts to ensure everything is washed and drains. They spot two cars at a time, then the ground team re-couples them, an engineer pulls them forward, then the next two are uncoupled, wheels chocked, and brakes, flags, and derails are set before starting the process again.
“Since Jason had the experience, he worked above the cars himself,” Baldwin said. “The others worked the ground and moved cars. They took on a job they weren’t familiar with but were eager to get it done for the customer.”
The group was able to wash 24 railcars before the temperature dropped enough to become hazardous and began affecting equipment. Their progress was able to prevent any shutdowns and ensure the next crew wasn’t facing a backlog.
“When they volunteered, I was like, ‘You realize it’s freezing and you’ll be soaking wet?’ They said they’d be cold whether they were just switching or washing and wanted to make sure the customer could keep operating,” Baldwin said. “They didn’t hesitate to jump in and get it done.”