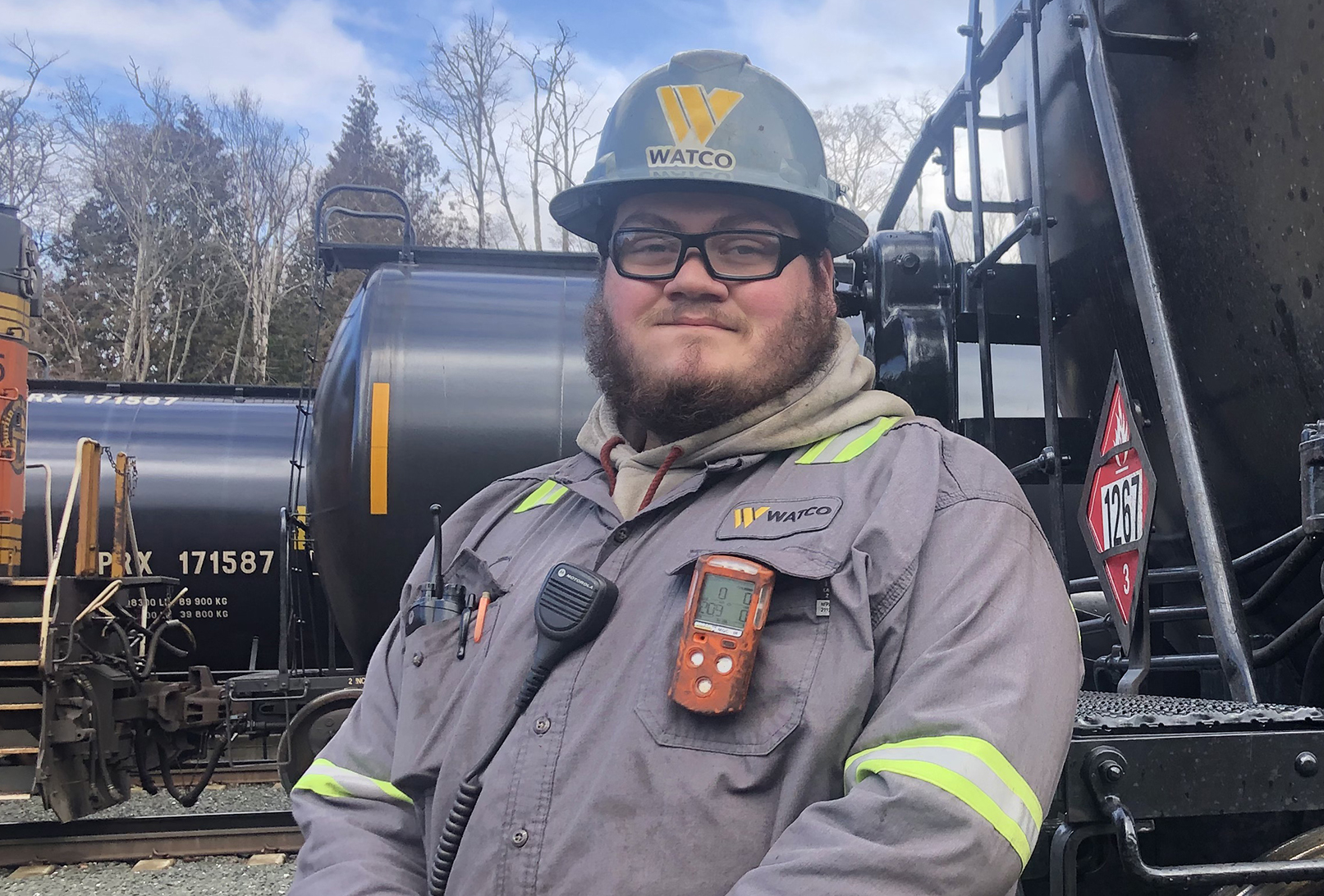
Conductor Takes on the Dirty Work
JUNE 2023 — Crude oil. No matter who you ask, you will find various descriptions, and most of them don’t make it sound too clean. And crude oil sludge? Well, it’s just how it sounds.
Although sludge is normally not an issue, it’s at its worst before or after cold weather, when things start to thicken or thaw. At that time of year, it can make trouble for team members everywhere. Not only can it make a train offload slick and messy, it can also disrupt an operation due to the time it takes to keep equipment clean.
At the Watco-operated customer terminal in Ferndale, Washington, no matter what they deal with, they take safety and housekeeping seriously. They ensure that equipment is in good working order and clean. That includes equipment important to spill containment: drip pans.
This year was no different when the weather there started to affect operations.
A unit train of crude oil arrived recently that put the Ferndale team to the test. And when that happened, Conductor Zach Eriksen took it upon himself to get ahead of the sludge so his teammates could focus on hooking up tank cars.
Cars on the first half of the train were secured at the unloading rack ready to be offloaded. These cars were hooked up with adapters and hoses on the bottom of the car and with drip pans under each one, just in case. The first half was offloaded with no issues.
After offloading oil from the cars, team members uncoupled the hoses and carefully removed the adapters from the outlet valves only to face the sludge. Most of the time, it’s never an issue, but sometimes, no matter how careful the team is, sludge can gum things up and make a mess of the adapters and the drip pans.
That’s when Eriksen stepped up.
As Terminal Manager Thomas Frey explained, there is normally a first crew hooking up hoses, unloading oil, unhooking hoses, and cleaning as they go in preparation for the next crew to repeat the process. But to help keep this offload on schedule, Eriksen had an idea. As Frey tells it, Eriksen “had a plan in his head on how to deal with the sludge. While the team hooked up the second set of cars for unload, Zach had them skip the messy ones. He then went behind them cleaning up the mess and hooking up the cars that he could. Instead of dumping it onto the second crew to clean it up, he said, ‘I’ll take care of the mess.’”
The team hooked up each car, skipping over the messy ones, while Zach cleaned those himself. By the time the team had reached the end of the string of cars, Zach had all the messy ones cleaned, and the team was able to double back and hook up any remaining cars.
Said Frey: “His actions improved our safety and the team’s morale, and prevented delays to the offload. By taking the lead and cleaning up, Zach made what could have been a longer and messier hook-up more productive for the team and the customer. He led by example and showed Watco’s Foundation Principles by valuing the customer, valuing the team, and safely improving every day.”